In today’s rapidly evolving work environment, organizations are continuously searching for innovative ways to boost efficiency and productivity. Among the most impactful strategies adopted globally is the 5S framework. Originating in Japan as a cornerstone of Lean manufacturing, this methodology emphasizes the importance of maintaining a clean, organized, and efficient workspace. By integrating the 5S principles into daily operations, businesses can streamline processes, reduce waste, enhance safety, and foster a culture of continuous improvement. This systematic approach not only transforms workspaces but also empowers employees to contribute meaningfully to organizational success.
The 5S methodology is built on five foundational pillars: Sort, Set in Order, Shine, Standardize, and Sustain. Each of these principles plays a pivotal role in optimizing workplace efficiency. Beyond eliminating inefficiencies, the 5S framework enhances employee morale and ensures a safer working environment. As organizations strive to achieve excellence, understanding and implementing the 5S methodology can significantly elevate operational performance.
This article delves into the nuances of the 5S methodology, addressing frequently asked questions and offering actionable insights into its implementation. Whether you lead a small business or work within a large corporation, the 5S framework can be customized to align with your unique goals and objectives, driving tangible results.
Read also:Exploring The Life And Influence Of Neo Hous Wife
Understanding the 5S Methodology
The 5S methodology is a structured approach to workplace organization and standardization. Its name derives from five Japanese terms, each representing a critical step in the process:
- Sort (Seiri): Identifying and removing unnecessary items to create a clutter-free environment.
- Set in Order (Seiton): Arranging essential tools and materials in a logical and accessible manner to minimize delays.
- Shine (Seiso): Ensuring cleanliness and maintenance of the workspace to promote safety and efficiency.
- Standardize (Seiketsu): Establishing consistent practices and protocols to sustain the first three S's.
- Sustain (Shitsuke): Cultivating a disciplined culture that ensures long-term adherence to 5S principles.
How the 5S Methodology Boosts Workplace Efficiency
Implementing the 5S methodology can significantly enhance workplace efficiency in several ways:
- Time Optimization: By organizing tools and materials effectively, employees spend less time searching for necessary items, allowing them to focus on productive tasks.
- Enhanced Safety: A well-organized and clean workspace minimizes the risk of accidents, ensuring a safer environment for all employees.
- Increased Morale: A tidy and structured workspace fosters a sense of pride and motivation among employees, leading to higher engagement and satisfaction.
- Improved Quality Control: Standardized processes result in consistent outcomes, ensuring higher quality outputs and reducing errors.
Steps to Successfully Implement the 5S Methodology
Adopting the 5S methodology requires a systematic and collaborative approach. Below are the essential steps to successfully integrate 5S into your organization:
- Employee Education: Conduct comprehensive training sessions to ensure all team members understand the significance and application of the 5S principles.
- Workspace Assessment: Thoroughly evaluate the current state of the workplace to identify areas that require improvement and prioritize them accordingly.
- Develop an Action Plan: Create a detailed roadmap outlining specific actions, timelines, and responsibilities to ensure a smooth implementation process.
- Engage Employees: Involve employees at every stage of the implementation to foster a sense of ownership and commitment to the 5S initiative.
- Continuous Monitoring: Regularly review progress and make necessary adjustments to ensure the effectiveness and sustainability of the 5S practices.
Is the 5S Methodology Suitable for All Industries?
The adaptability of the 5S methodology makes it applicable across a wide range of industries, including:
- Manufacturing: Streamlining production processes and minimizing waste to improve efficiency and reduce costs.
- Healthcare: Enhancing patient care by optimizing workflows, ensuring cleanliness, and improving operational efficiency.
- Office Environments: Creating a more organized and productive workspace that supports seamless collaboration and communication.
- Retail: Optimizing inventory management, improving customer experience, and enhancing store aesthetics to boost sales.
Potential Challenges in Implementing the 5S Methodology
While the benefits of the 5S methodology are undeniable, organizations may encounter challenges during implementation. These challenges include:
- Resistance to Change: Employees may feel uneasy about adopting new processes, especially if they perceive them as additional burdens.
- Lack of Leadership Support: Without strong commitment from leadership, 5S initiatives may struggle to gain traction or sustain long-term success.
- Inadequate Training: Insufficient understanding of the 5S principles can hinder effective implementation and lead to inconsistent results.
Ensuring Long-Term Success with the 5S Methodology
To ensure the sustained effectiveness of 5S practices, organizations can adopt the following strategies:
Read also:Exploring Neal Bledsoes Life Career And Partner
- Regular Audits: Conduct periodic assessments to monitor adherence to 5S standards and identify areas for improvement.
- Ongoing Training and Support: Provide continuous education and resources to employees, reinforcing their understanding and application of 5S principles.
- Culture of Discipline: Foster a culture of accountability and continuous improvement by encouraging employees to take ownership of the 5S process.
Conclusion: The Value of Implementing the 5S Methodology
In summary, the 5S methodology provides a robust framework for organizations seeking to enhance efficiency, safety, and employee morale. By embracing the principles of Sort, Set in Order, Shine, Standardize, and Sustain, businesses can create a more productive and organized workplace environment. While initial implementation may require dedication and effort, the long-term benefits far outweigh the challenges. For any organization committed to improving its operations, integrating the 5S methodology is a strategic investment that promises lasting success. If you're ready to elevate your business, consider adopting the 5S methodology today.

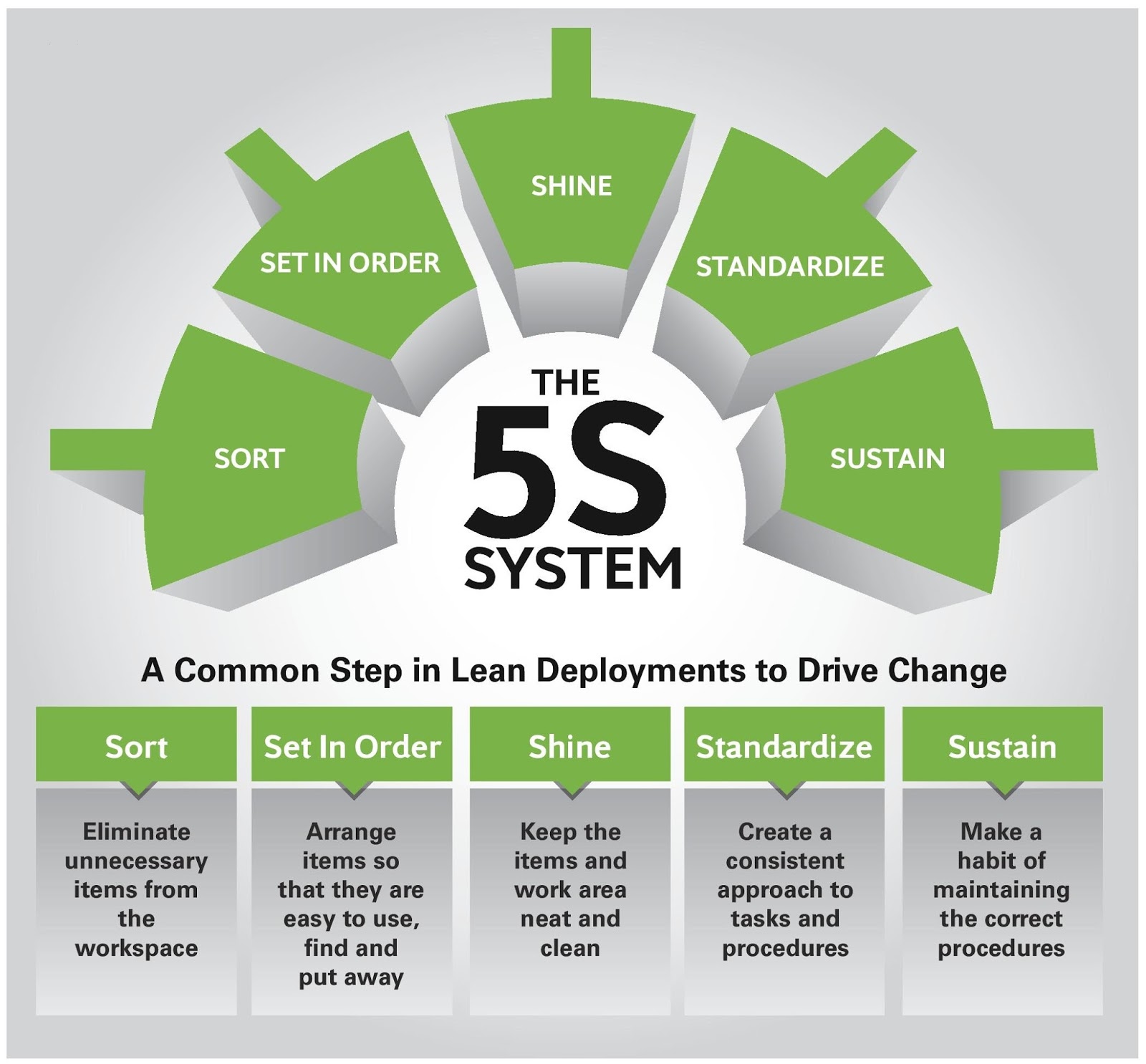